Material
Inconel 625 alloy is a non-magnetic, corrosion – and oxidation-resistant Ni-Cr alloy. The high strength of Inconel 625 is the result of the hardening of molybdenum and niobium on the nickel-chromium matrix of the alloy. Inconel 625 is extremely resistant to a variety of exceptionally severe corrosive environments, including high-temperature action (e.g., oxidation and carburizing), including corrosion. Its excellent strength and toughness are mainly due to the solution of refractory metals Co and molybdenum in nichcr matrix in the high temperature range from low temperature to up to 2000°F (1093°C). Nichcr 625 offers excellent resistance to pitting and crevice corrosion, high corrosion fatigue strength, high tensile strength, and resistance to stress corrosion cracking by chloride ions — making it an excellent choice for seawater applications. Inconel is used in aerospace applications as well as Marine applications. Common applications of this alloy are springs, seals, bellows for diving controllers, cable connectors, fasteners, flexible devices, and oceanographic instrument assemblies. Inconel 625 is a high-strength, highly corrosion-resistant nickel-chrome-molybdenum alloy used in the aerospace, oil and gas, automotive, Marine, chemical processing and nuclear industries.
Performance
The alloy is a solid solution strengthened nickel base deformation superalloy with molybdenum niobium as the main strengthening element. It has excellent corrosion resistance and oxidation resistance. It has good tensile and fatigue properties from low temperature to 980℃, and is resistant to stress corrosion under salt spray atmosphere. Therefore, it can be widely used in the manufacture of aircraft engine parts, aerospace structural parts and chemical equipment.
Technology
1.the alloy has good cold and hot formability, steel ingot forging heating temperature 1120℃.
2.The average grain size of the alloy is closely related to the deformation degree and final forging temperature of the forging.
3.the welding performance of the alloy is good, can be used in a protective atmosphere with tungsten pole or the alloy as a filler for argon arc welding, also available brazing connection and resistance seam welding.
4.surface treatment process: remove the oxide skin on the surface of the alloy first alkali washing, and then pickling in acid, hydrofluoric acid – water solution.
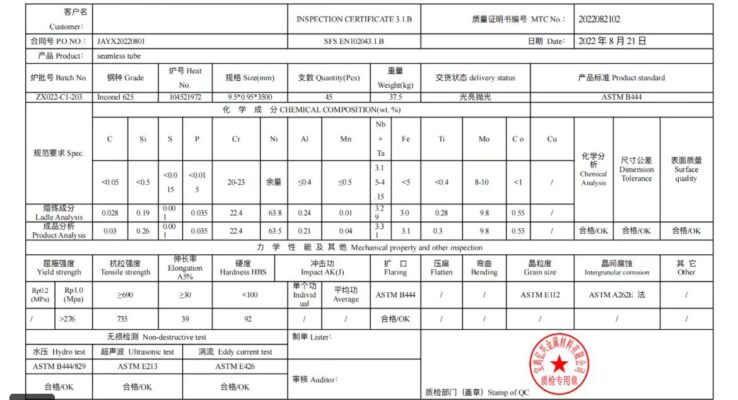